
By Vikky Leung Ramos
The North Satellite Modernization Project is the expansion and renovation of an almost 50-year-old building. When the Port of Seattle and Alaska Airlines open this new building in the summer of 2021, it will be a bigger and brighter space with 20 boarding gates and more dining and retail options.
When you come into the new building that houses the N gates, you will assuredly be taken by the high ceilings, Pacific Northwest inspired artwork, and all the updated and open views. Unlike the window walls and the spacious, bright waiting areas, you won’t notice the crucial building performance testing to complete this facility and ready it for the public.
Here, we chat with NSAT Project Manager Frederick Robinson and Resident Engineer Anne Timmermans, for a behind-the-scenes view of how the SEA Airport team tests a new facility to ensure that it’s safe, sustainable, and ready for its debut.
Step 1: Smoke control test
Safety first! The smoke control test is a building code requirement, but a safeguard that we hope is never needed. The NSAT has its own Very Early Smoke Detection Apparatus (VESDA). VESDA is an advanced smoke-detection trigger alarm that, in the earliest detection of a fire, directs the building’s air supply systems to shift from normal heating and air conditioning into smoke control mode. It will contain the smoke and control how it moves while closing off other vents so that the smoke does not travel to different parts of the building. VESDA can pinpoint the exact zone of where a fire is located, measure if the fire is getting worse, alert the authorities, and signaling the sprinkler and evacuation systems.
For VESDA to be tested, we run various sequences with the Port Fire Department such as opening an actual can of smoke to simulate a fire event. “Within minutes, VESDA will alert the appropriate units to respond and tell you if the system is working,” Robinson explains. “Testing is done at night to ensure there’s no impact to the traveling public.”
Step 2: Building leaks test
NSAT is one of the most sustainable projects in the airport’s history. The Port aspires to be the greenest Port in North America, and this building takes us a step closer to that goal through energy efficiency, architectural design, and sustainable building materials.
Another critical test in completing the NSAT double checks that no part of the building’s “skin” — the roof, windows, and exterior walls — have accidental conditions that allow air inside the building to leak out. This guarantees that the building is as energy efficient as possible. Reducing air leaks prevents the cool air from seeping out on a hot summer day and keeps warm air indoors on colder nights.
To assess the amount of air leakage, the SEA team closes all known ways that air can escape from the building and turns up the building air handling units. Robinson compares this to blowing up a big balloon. With the building essentially inflated, the pressure inside will look for ways to escape. As in the previous test, smoke can be used and followed to see if there are any places that are leaking.
An infrared gun can also be used to detect air leaks. This method measures the air temperature inside; the infrared technology can show if any building-temperature air is escaping into the outside air and helps to pinpoint the location of any leaks.
NSAT is built with an expected 50-year life cycle, so this test is vital to understanding the building’s likely energy performance. If a leak does appear, it can be fixed immediately to avoid major surprises or damages down the road. “Ten years from now or beyond, this building should not experience any weather issues with condensation, mold, or outside air affecting the ambient temperatures,” Timmermans says.
This test is done throughout the day and as a traveler, you won’t even know it. “Passengers will not notice anything more than a very faint whistling from the HVAC,” added Robinson.
Step 3: Air quality test
After the team verifies that all the building codes are met, a third and final test is performed to completely clean the air. One inevitable result of construction is particulates like dust that need to be flushed out of the facility. To achieve this, the building’s air handling units are turned up over several weeks to increase the volume of air pushed through the building and keep it circulating.
“Once the required amount of air is pumped into the building, any contaminants from construction activities floating through the air are flushed out,” said Timmermans. “This is how the project meets the LEED criteria for enhanced indoor air quality. When passengers travel through and use the new spaces, there should be no smells like plastic, paint fumes, or dust particles noticed.”
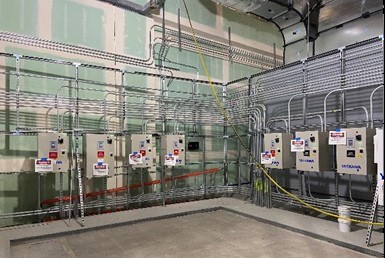
handling units that control how much air gets put where.
Step 4: Air filtration
The final step is to replace the last of the used air filters before the space is ready to be turned over for operational use.
Completing this project is a major accomplishment, especially while grappling with a pandemic. Robinson and Timmermans both describe this as a “mega team effort” to build and test this world-class airport facility. “The fact that the Port takes time to run these tests — multiple tests — illustrates that everyone believes in this work and cares about the Port’s commitment to sustainability,” said Robinson.
Subscribe to the Nuts & Bolts newsletter for construction news.